CAE ANALYSIS
Structural stress analysis based on FEA
Stress analysis based on FEA enables comprehensive modeling and efficient optimization of complex structural behaviors such as material fatigue and creep.
Most practical stress analysis based on FEA uses linear material models with nonlinear contact. Results Engineering offers a full range of capabilities including highly nonlinear materials such as rubber and composites, complex contacts, and complex large-displacement problems. Results Engineering also has full experience in performing structural analyses using modern FEA methods for numerous construction standards (ISO, BS, ASCE, ASME, MIL, DIN).
case studies
FEA Fatigue Analysis of Electric AGV for Simworx Ltd.
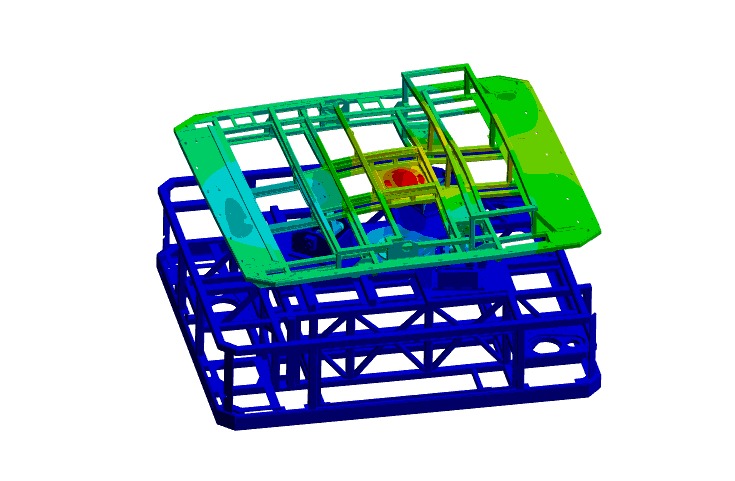
A top UK-based amusement park attractions supplier approached us to validate the structural integrity of their new electric Automated Guided Vehicle (AGV). Using Finite Element Analysis (FEA), we conducted a comprehensive assessment to ensure the design met the stringent requirements of Eurocode 3.
Our analysis provided critical insights into load-bearing capacity, stress distribution, and structural performance, allowing the client to confidently move forward with a design that is both safe and compliant. This project highlights our expertise in applying advanced simulation techniques to innovative engineering solutions.
Optical Simulation of Hotel Recreational Area in direct Sun
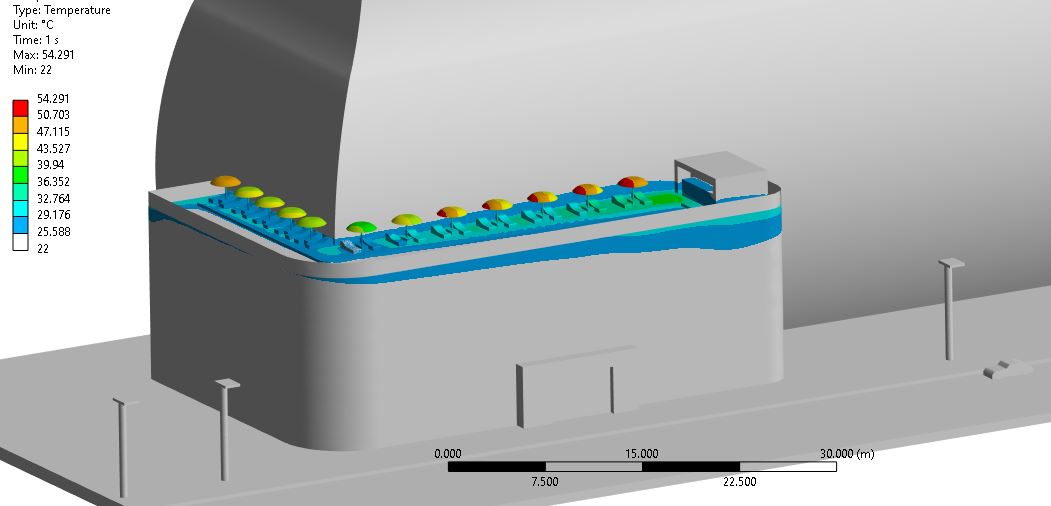
Optical simulations are widely implemented in the construction industry. Especial today when glazing is taking more and more space on the facades.
This glazing can act as mirror to focus sun energy in one area called focal points. Here we can see multiple snapshots thou-out a day to investigate how sun is moving in relation to the buildings features.
Great example for how technology can be used to predict solar irradiance and temperature at hotel swimming pool deck. This unique simulation combines optical simulation with thermal simulations.
Highlighting sun hot spots to civil engineers and architects to work around them or selecting materials that will absorb or disperse energy.
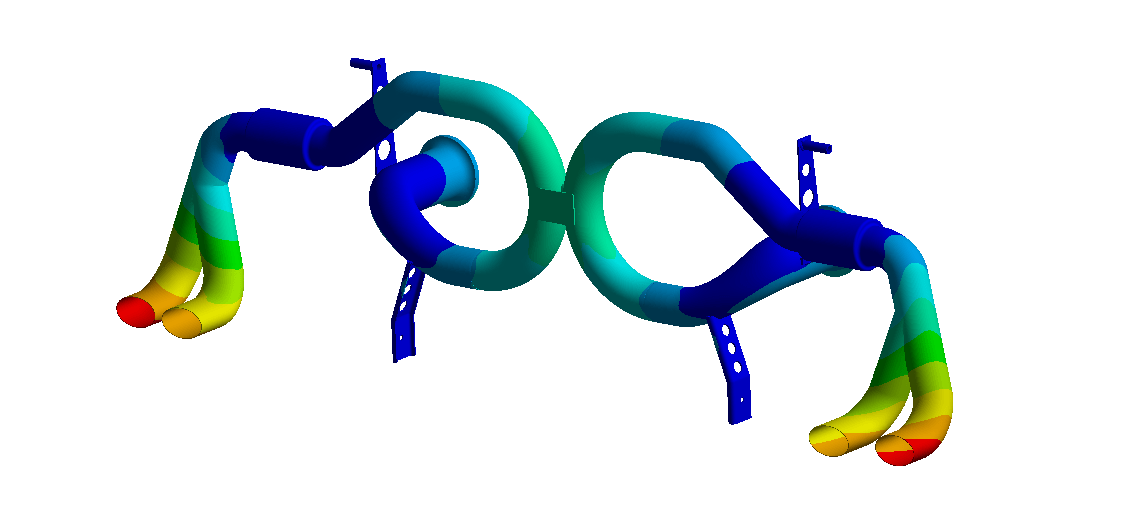
Multi-physics CAE Simulation incorporating CFD, Heat and Fatigue Analysis
One of our recent project, we conducted a comprehensive fatigue analysis of an exhaust system to ensure long-term reliability under extreme operating conditions. Our approach involved a three-step methodology:
- Computational Fluid Dynamics (CFD) – Simulated exhaust gas flow to determine temperature distribution and pressure variations.
- Finite Element Analysis (FEA) – Heat Analysis – Evaluated thermal loads and material responses to prolonged high-temperature exposure.
- Thermal Stress Estimation – Assessed the combined effects of thermal expansion and mechanical stresses to predict fatigue life.
Our analysis provided key design recommendations to mitigate fatigue failure, optimize material selection, and enhance durability, ensuring the system meets performance and safety requirements.
Tracked Machine Motion Analysis for Optimized Performance
For a recent project, we conducted a detailed motion analysis of a tracked machine to assess its performance under real-world operating conditions. By leveraging advanced simulation techniques, we provided valuable insights that optimized torque requirements, ensured pre-build validation, and refined loading specifications—all contributing to cost savings and efficiency improvements.
360 Excavator Machine Motion Analysis material handling
For a recent project, we conducted a detailed motion analysis of a tracked machine to assess its performance under real-world operating conditions. By leveraging advanced simulation techniques, we provided valuable insights that optimized torque requirements, ensured pre-build validation, and refined loading specifications—all contributing to cost savings and efficiency improvements.
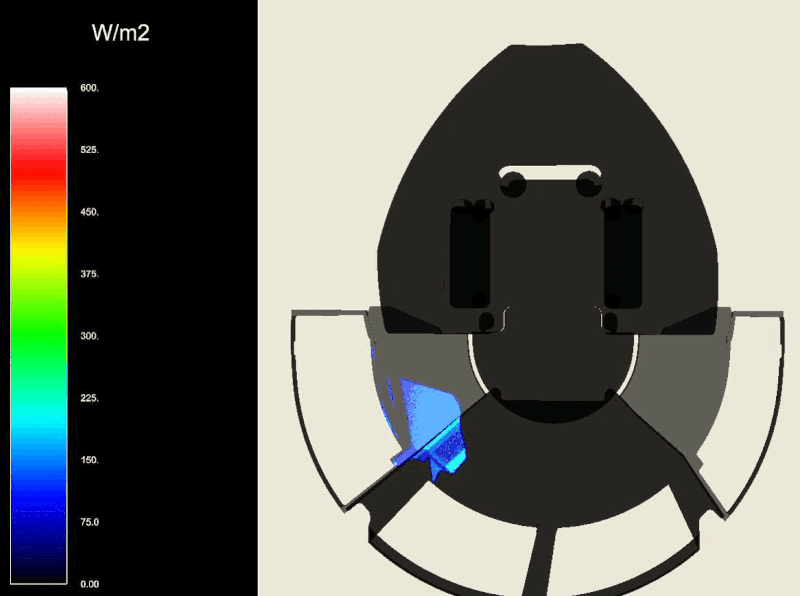
Optimizing Sunlight Exposure in Next-Gen Electric Machine Cabin
We’re excited to share insights from our latest optical simulation of sun tracking for a start-up developing electric earth-moving machine cabins!
Using advanced simulation techniques, we conducted a detailed irradiance analysis to evaluate how sunlight interacts with the cabin interior throughout the day. GIFs with irradiance maps illustrate how we examined sun exposure from dawn to dusk, identifying potential hotspots and worst-case scenarios.
🔹 Key Finding: No significant focal points of concern, with interior trim temperatures staying within safe limits.
🔹 Impact: This simulation-driven approach enables us to proactively assess heat exposure risks, ensuring optimal material selection for long-term durability and comfort.
By leveraging these insights, we’re shaping the next generation of efficient, comfortable, and resilient electric machine cabins.
Stress Analysis